多くの場合、MIG ガンの消耗品は溶接プロセスにおいて後回しになる可能性があります。これは、溶接オペレータ、監督者、および作業に関与するその他の人々の注意を、機器、ワークフロー、部品設計などに関する懸念が支配しているためです。しかし、これらのコンポーネント、特にコンタクトチップは、溶接のパフォーマンスに大きな影響を与える可能性があります。
MIG 溶接プロセスでは、コンタクト チップはワイヤがボアを通過する際に溶接電流をワイヤに伝達し、アークを生成する役割を果たします。最適には、ワイヤは電気的接触を維持しながら最小限の抵抗で通過する必要があります。コンタクトチップ凹部と呼ばれる、ノズル内のコンタクトチップの位置も同様に重要です。溶接作業の品質、生産性、コストに影響を与える可能性があります。また、作業全体のスループットや収益性に寄与しない部品の研削やブラストなど、付加価値のない作業の実行に費やす時間にも影響する可能性があります。
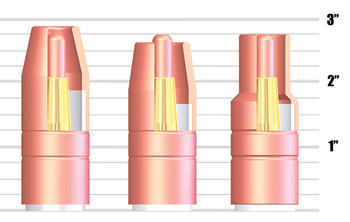
正しいコンタクトチップの凹みは用途によって異なります。通常、ワイヤの突き出しが少ないとアークがより安定し、低電圧貫通が向上するため、最適なワイヤの突き出し長さは、一般にアプリケーションで許容される最も短い長さになります。
溶接品質への影響
コンタクトチップの凹みは、溶接の品質に影響を与える可能性のある多くの要因に影響を与えます。たとえば、突き出しや電極の延長 (コンタクト チップの端と作業面の間のワイヤの長さ) は、コンタクト チップの凹みによって異なります。具体的には、コンタクト チップの凹みが大きいほど、ワイヤの突き出しも長くなります。ワイヤの突き出しが増加すると、電圧が増加し、アンペア数が減少します。これが発生すると、アークが不安定になり、過剰なスパッタ、アークのふらつき、薄い金属の熱制御不良、および移動速度の低下を引き起こす可能性があります。
コンタクトチップの凹みも溶接アークからの輻射熱に影響します。熱が蓄積すると、フロントエンドの消耗品の電気抵抗が増加し、ワイヤに電流を流すコンタクトチップの能力が低下します。この導電性の低下により、不十分な溶け込み、スパッタ、その他の問題が発生し、許容できない溶接が発生したり、やり直しが必要になったりする可能性があります。
また、熱が高すぎると、一般にコンタクト チップの寿命が短くなります。その結果、全体的な消耗品のコストが高くなり、コンタクトチップの交換にかかるダウンタイムが長くなります。溶接作業ではほとんどの場合、人件費が最大のコストとなるため、ダウンタイムが積み重なると生産コストが不必要に増加する可能性があります。
コンタクトチップの凹みによって影響を受けるもう 1 つの重要な要素は、シールドガスの適用範囲です。コンタクトチップの凹部によりノズルがアークや溶接溜まりから遠く離れた位置にあると、溶接領域はシールドガスを乱したり置換したりする可能性のある気流の影響を受けやすくなります。シールドガスの適用範囲が不十分だと、多孔性、スパッタ、不十分な浸透が発生します。
これらすべての理由から、用途に応じて正しいコンタクト リセスを利用することが重要です。いくつかの推奨事項が続きます。
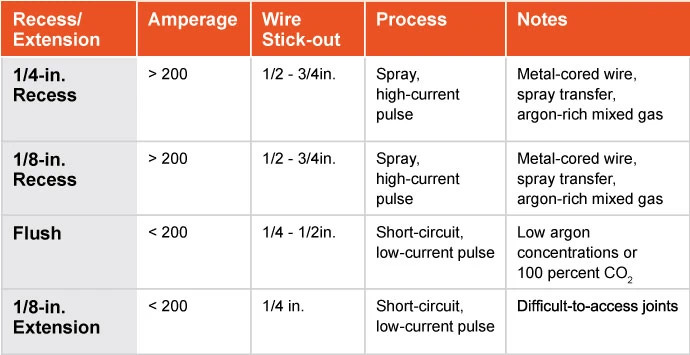
図 1: 正しいコンタクト チップの凹みは用途によって異なります。作業に適したコンタクトチップの凹みを決定するには、必ずメーカーの推奨事項を参照してください。
コンタクトチップの凹みの種類
ディフューザー、チップ、ノズルは、MIG ガンの消耗品を構成する 3 つの主要な部品です。ディフューザーはガンのネックに直接取り付けられ、電流をコンタクトチップに流し、ガスをノズルに送ります。チップはディフューザーに接続されており、ワイヤーがノズルを通って溶接溜まりに誘導されるときに、ワイヤーに電流を伝えます。ノズルはディフューザーに取り付けられており、シールド ガスを溶接アークと水たまりに集中させ続ける役割を果たします。各コンポーネントは溶接全体の品質において重要な役割を果たします。
MIG ガンの消耗品には、固定式と調整式の 2 種類のコンタクト チップ リセスが用意されています。調整可能なコンタクトチップの凹部は、さまざまな範囲の深さと延長に変更できるため、さまざまな用途やプロセスの凹部の需要を満たすことができるという利点があります。ただし、溶接オペレータはノズルの位置を操作したり、コンタクトチップを所定の凹部に固定するロック機構を介して調整するため、人的ミスが発生する可能性も高くなります。
ばらつきを防ぐために、溶接の均一性を確保し、どの溶接オペレータでも一貫した結果を達成する方法として、一部の企業は固定リセスチップを好んでいます。固定凹部チップは、一貫したチップ位置が重要な自動溶接用途では一般的です。
さまざまなメーカーがさまざまなコンタクトチップの凹みの深さに対応する消耗品を製造しています。通常、その深さは 1/4 インチの凹みから 1/8 インチの延長部までの範囲です。
正しいリセスの決定
正しいコンタクトチップの凹みは用途によって異なります。考慮すべき良いルールは、ほとんどの条件下で、電流が増加するとリセスも増加するということです。また、ワイヤの突き出しが少ないと、通常、アークがより安定し、低電圧貫通が向上するため、最適なワイヤの突き出し長さは、一般に、用途に許容できる最も短い長さになります。以下にいくつかのガイドラインを示します。追加の注意事項については、図 1 も参照してください。
1. パルス溶接、スプレー転写プロセス、および 200 アンペアを超えるその他の用途では、1/8 インチまたは 1/4 インチのコンタクト チップの凹みを推奨します。
2. 厚い金属を大径ワイヤまたはスプレー転写プロセスでメタルコアワイヤと接合するような高電流のアプリケーションの場合、凹型コンタクトチップはコンタクトチップをアークの高熱から遠ざけるのにも役立ちます。これらのプロセスに長いワイヤの突き出しを使用すると、バーンバック (ワイヤが溶けてコンタクト チップに焼き付く) やスパッタの発生が軽減され、コンタクト チップの寿命が延長され、消耗品コストが削減されます。
3. 短絡転写プロセスまたは低電流パルス溶接を使用する場合は、通常、ワイヤ突き出し量が約 1/4 インチのフラッシュ コンタクト チップを推奨します。比較的短い突き出し長さにより、焼き付きや反りの危険を冒すことなく、低スパッタで薄い材料を溶接するための短絡転写が可能になります。
4.拡張コンタクトチップは通常、パイプ溶接における深くて狭いV溝ジョイントなど、アクセスが困難なジョイント構成を備えた非常に限られた数の短絡アプリケーション用に予約されています。
これらの考慮事項は選択に役立ちますが、作業に適したコンタクト チップの凹みを決定するには、常にメーカーの推奨事項を参照してください。正しい位置に配置すると、過剰なスパッタ、多孔性、不十分な浸透、薄い材料での焼き付きや反りなどが発生する可能性が低減されることに注意してください。さらに、企業がコンタクトチップの凹みがそのような問題の原因であると認識すると、時間とコストのかかるトラブルシューティングや再作業などの溶接後の作業を排除するのに役立ちます。
追加情報: 高品質のヒントを選択する
コンタクト チップは高品質の溶接を完了し、ダウンタイムを短縮するための重要な要素であるため、高品質のコンタクト チップを選択することが重要です。これらの製品は、低グレードの製品よりも価格が若干高い場合がありますが、寿命を延ばし、切り替え時のダウンタイムを削減することで長期的な価値を提供します。さらに、高品質のコンタクト チップは改良された銅合金から作られており、通常は機械公差が厳しくなるように機械加工されており、より優れた熱的および電気的接続を実現して熱の蓄積と電気抵抗を最小限に抑えます。高品質の消耗品は通常、より滑らかな中心穴を備えており、ワイヤが通過する際の摩擦が少なくなります。つまり、抵抗が少なく、潜在的な品質問題が少なく、安定したワイヤ供給が可能になります。高品質のコンタクトチップは、バーンバックを最小限に抑え、不均一な導電率によって引き起こされる異常なアークの防止にも役立ちます。
投稿時刻: 2023 年 1 月 1 日