MIG 溶接は、他のプロセスと同様に、スキルを磨くには練習が必要です。初めての方は、基本的な知識を身につけることで、MIG 溶接作業を次のレベルに引き上げることができます。または、しばらく溶接を行っている場合は、リフレッシュすることは決して悪いことではありません。これらのよくある質問とその回答は、溶接のヒントとして参考にしてください。
1. どのドライブロールを使用すればよいですか?また、テンションはどのように設定すればよいですか?
溶接ワイヤのサイズと種類によって、スムーズで安定したワイヤ送給を実現するための駆動ロールが決まります。一般的な選択肢は、V ローレット、U 溝、V 溝の 3 つです。
ガスシールドまたはセルフシールドワイヤを V ローレットドライブロールと組み合わせます。これらの溶接ワイヤは管状の設計のため柔らかいです。ドライブ ロールの歯がワイヤを掴み、フィーダ ドライブに押し込みます。アルミ溶接ワイヤの送給にはU溝駆動ロールをご使用ください。これらの駆動ロールの形状は、この柔らかいワイヤーの損傷を防ぎます。V 溝ドライブロールはソリッドワイヤに最適です。
ドライブ ロールの張力を設定するには、まずドライブ ロールを解放します。手袋をした手にワイヤーを送り込みながら、ゆっくりと張力を高めます。張力がワイヤーの滑りを超えて半回転するまで続けます。プロセス中は、ワイヤの供給不良につながる可能性があるケーブルのよじれを避けるために、ガンをできるだけ真っすぐに保ってください。

溶接ワイヤ、ドライブ ロール、およびシールド ガスに関連するいくつかの主要なベスト プラクティスに従うと、MIG 溶接プロセスで良好な結果を確実に得ることができます。
2. MIG 溶接ワイヤから最良の結果を得るにはどうすればよいですか?
MIG 溶接ワイヤの特性と溶接パラメータは異なります。常にワイヤの仕様またはデータシートを確認して、溶加材メーカーが推奨するアンペア数、電圧、ワイヤ送り速度を確認してください。通常、仕様シートは溶接ワイヤに同梱されていますが、溶加材製造元の Web サイトからダウンロードすることもできます。これらのシートには、シールド ガス要件のほか、接触部から作業部までの距離 (CTWD) および溶接ワイヤの延長または突き出しに関する推奨事項も記載されています。
最適な結果を得るには、スティックアウトが特に重要です。突き出しが長すぎると、溶接部が冷たくなり、アンペア数が低下し、接合部の貫通力が低下します。通常、スティックアウトが短いほど、アークがより安定し、低電圧貫通が向上します。経験則として、最適な突き出し長さは、アプリケーションで許容される最短の長さです。
良好な MIG 溶接結果を得るには、溶接ワイヤの適切な保管と取り扱いも重要です。湿気によりワイヤが損傷し、水素による亀裂が発生する可能性があるため、スプールは乾燥した場所に保管してください。ワイヤーを扱うときは、湿気や手の汚れから保護するために手袋を使用してください。ワイヤがワイヤ送給装置上にあるが使用していない場合は、スプールをカバーするか、取り外して清潔なビニール袋に入れます。
3. どのコンタクトリセスを使用すればよいですか?
コンタクト チップの凹み、または MIG 溶接ノズル内のコンタクト チップの位置は、使用する溶接モード、溶接ワイヤ、用途、シールド ガスによって異なります。一般に、電流が増加すると、コンタクトチップの凹みも増加します。ここにいくつかの推奨事項があります。
1/8 または 1/4 インチのくぼみは、メタルコア ワイヤとアルゴンを多く含むシールド ガスを使用する場合、スプレー溶接または高電流パルス溶接で 200 アンペアを超える溶接に適しています。このようなシナリオでは、1/2 ~ 3/4 インチのワイヤ 突き出しを使用できます。
短絡または低電流パルス モードで 200 アンペア未満で溶接する場合は、コンタクト チップをノズルと同一面に保ってください。1/4 ~ 1/2 インチのワイヤ突き出しを推奨します。特に、短絡時の突き出しが 1/4 インチなので、焼き抜けや反りのリスクを減らして、より薄い材料を溶接できます。
届きにくい接合部を 200 アンペア未満で溶接する場合は、コンタクト チップをノズルから 1/8 インチ延長し、1/4 インチのスティックアウトを使用できます。この構成により、アクセスが困難なジョイントへのアクセスが容易になり、短絡または低電流パルス モードに適しています。
適切なリセスは、多孔性、不十分な浸透、溶け込みの可能性を減らし、スパッタを最小限に抑えるための鍵であることを忘れないでください。
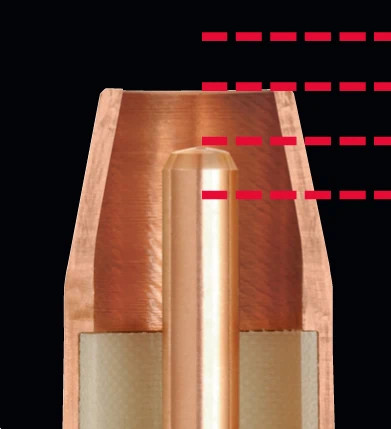
理想的なコンタクトチップの凹み位置は用途によって異なります。一般的なルール: 電流が増加すると、凹みも増加する必要があります。
4. MIG 溶接ワイヤに最適なシールドガスは何ですか?
選択するシールドガスは、ワイヤと用途によって異なります。CO2 は厚い材料を溶接するときに優れた浸透性をもたらし、より低温になる傾向があり、焼き付きのリスクを軽減するため、薄い材料にも CO2 を使用できます。溶接の溶け込みをさらに高め、生産性を高めるには、75 パーセントのアルゴンと 25 パーセントの CO2 混合ガスを使用します。この組み合わせでは、CO2 よりもスパッタの発生が少ないため、溶接後の清掃が少なくなります。
100 パーセント CO2 シールド ガス、または 75 パーセント CO2/25 パーセント アルゴン混合ガスを炭素鋼ソリッド ワイヤと組み合わせて使用します。アルミニウム溶接ワイヤにはアルゴン シールド ガスが必要ですが、ステンレス鋼ワイヤはヘリウム、アルゴン、CO2 の 3 つの混合物で最もよく機能します。推奨事項については、必ずワイヤーの仕様シートを参照してください。
5. 溶接溜まりを制御する最善の方法は何ですか?
どの位置でも、溶接ワイヤを溶接だまりの先端に向けておくのが最善です。位置をずらして(垂直、水平、頭上)溶接する場合は、溶接溜まりを小さく保つことが最適な制御になります。また、溶接接合部を十分に埋めることができる最小のワイヤ直径を使用します。
生成される溶接ビードによって入熱と移動速度を測定し、それに応じて調整して、より良い制御とより良い結果を得ることができます。たとえば、溶接ビードが高すぎて細い場合は、入熱が低すぎたり、移動速度が速すぎたりすることを示しています。平らで幅の広いビードは、熱入力が高すぎるか、移動速度が遅すぎることを示唆しています。それに応じてパラメータとテクニックを調整して、周囲の金属にちょうど接触するわずかなクラウンを持つ理想的な溶接を実現します。
よくある質問に対するこれらの回答は、MIG 溶接のベスト プラクティスのほんの一部についてのみ触れています。最適な結果を得るには、常に溶接手順に従ってください。また、多くの溶接機器やワイヤのメーカーには、質問に対応できるテクニカル サポート番号が用意されています。それらはあなたにとって優れたリソースとして役立ちます。
投稿時刻: 2023 年 1 月 2 日